Budowa maszyn pneumatycznych opiera się na kilku kluczowych elementach, które współpracują ze sobą w celu efektywnego działania systemu. Podstawowym komponentem jest sprężarka, która odpowiada za kompresję powietrza i dostarczanie go do układu. Sprężarki mogą być różnego rodzaju, w tym tłokowe, śrubowe czy wirnikowe, a ich wybór zależy od wymagań aplikacji. Kolejnym istotnym elementem są zbiorniki powietrza, które służą do magazynowania skompresowanego powietrza i zapewniają stabilność ciśnienia w systemie. W maszynach pneumatycznych niezbędne są również zawory, które kontrolują przepływ powietrza oraz jego kierunek. Zawory te mogą być ręczne lub automatyczne, a ich dobór ma kluczowe znaczenie dla efektywności całego układu. Dodatkowo, siłowniki pneumatyczne zamieniają energię sprężonego powietrza na ruch mechaniczny, co pozwala na wykonywanie różnych zadań. Warto również wspomnieć o filtrach i osuszaczach, które oczyszczają powietrze z zanieczyszczeń oraz wilgoci, co jest niezwykle ważne dla prawidłowego funkcjonowania maszyn.
Jakie są zastosowania maszyn pneumatycznych w przemyśle
Maszyny pneumatyczne znajdują szerokie zastosowanie w różnych gałęziach przemysłu dzięki swojej wszechstronności i efektywności. W przemyśle produkcyjnym wykorzystuje się je do automatyzacji procesów montażowych, gdzie siłowniki pneumatyczne umożliwiają precyzyjne pozycjonowanie i ruchy robocze. Dzięki swojej szybkości i niezawodności maszyny te są idealne do linii produkcyjnych, gdzie czas reakcji jest kluczowy. W branży motoryzacyjnej maszyny pneumatyczne stosowane są do lakierowania oraz obróbki powierzchniowej, co pozwala na uzyskanie wysokiej jakości wykończenia produktów. Kolejnym przykładem zastosowania jest pakowanie towarów, gdzie pneumatyczne systemy transportowe przyspieszają procesy logistyczne. W sektorze spożywczym maszyny te są wykorzystywane do napełniania butelek oraz pakowania produktów, co zapewnia zachowanie higieny i bezpieczeństwa żywności. Ponadto w branży budowlanej maszyny pneumatyczne znajdują zastosowanie w narzędziach takich jak młoty udarowe czy wiertarki, które charakteryzują się dużą mocą i wydajnością.
Jakie są zalety korzystania z maszyn pneumatycznych
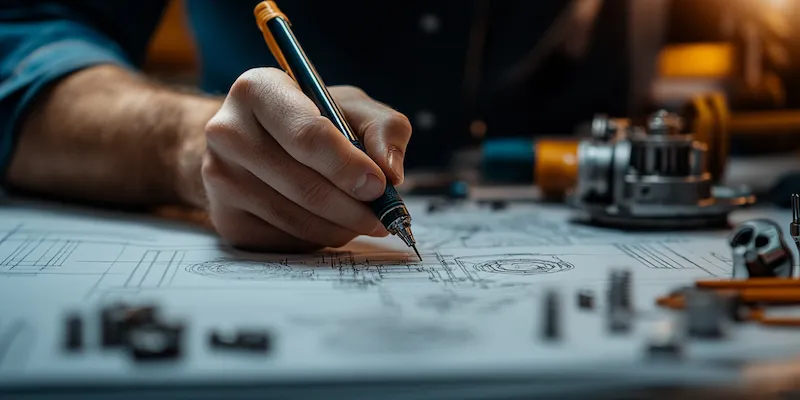
Korzystanie z maszyn pneumatycznych niesie ze sobą wiele korzyści, które przyczyniają się do zwiększenia efektywności procesów produkcyjnych. Jedną z głównych zalet jest ich prostota obsługi oraz łatwość w integracji z istniejącymi systemami produkcyjnymi. Maszyny te charakteryzują się także dużą niezawodnością i długą żywotnością, co sprawia, że są one ekonomicznym rozwiązaniem dla wielu przedsiębiorstw. Kolejnym atutem jest ich zdolność do pracy w trudnych warunkach środowiskowych, ponieważ nie wymagają one stosowania skomplikowanych układów elektrycznych czy hydraulicznych. Pneumatyka jest również bardziej bezpieczna niż inne systemy napędowe, ponieważ nie ma ryzyka wycieku oleju czy innych substancji chemicznych. Dodatkowo maszyny pneumatyczne generują mniejsze koszty eksploatacyjne związane z konserwacją i serwisowaniem, co czyni je bardziej atrakcyjnymi dla firm. Warto również zwrócić uwagę na ich elastyczność – można je łatwo dostosować do zmieniających się potrzeb produkcyjnych poprzez zmianę parametrów pracy lub dodanie nowych komponentów.
Jakie są najnowsze trendy w budowie maszyn pneumatycznych
W ostatnich latach obserwuje się dynamiczny rozwój technologii związanych z budową maszyn pneumatycznych, co wpływa na ich funkcjonalność oraz efektywność. Jednym z najważniejszych trendów jest automatyzacja procesów produkcyjnych poprzez integrację maszyn pneumatycznych z systemami robotyzacji oraz sztucznej inteligencji. Dzięki temu możliwe staje się osiągnięcie jeszcze wyższej precyzji oraz szybkości działania, co przekłada się na zwiększenie wydajności produkcji. Kolejnym istotnym kierunkiem rozwoju jest miniaturyzacja komponentów pneumatycznych, co pozwala na tworzenie bardziej kompaktowych rozwiązań idealnych do zastosowań w ograniczonej przestrzeni. Wprowadzenie nowoczesnych materiałów oraz technologii produkcji przyczynia się również do zwiększenia efektywności energetycznej maszyn pneumatycznych oraz redukcji kosztów eksploatacyjnych. Coraz większą uwagę przykłada się także do kwestii ekologicznych – projektanci starają się tworzyć rozwiązania minimalizujące zużycie energii oraz emisję hałasu podczas pracy urządzeń. W kontekście cyfryzacji przemysłu rośnie znaczenie monitorowania i diagnostyki stanu technicznego maszyn pneumatycznych za pomocą nowoczesnych czujników oraz systemów informacyjnych, co pozwala na szybsze wykrywanie usterek i optymalizację procesów serwisowych.
Jakie są najczęstsze problemy w budowie maszyn pneumatycznych
Budowa maszyn pneumatycznych, mimo wielu zalet, wiąże się również z występowaniem różnych problemów, które mogą wpływać na ich efektywność oraz niezawodność. Jednym z najczęstszych problemów jest nieszczelność układu, która może prowadzić do utraty ciśnienia i obniżenia wydajności maszyny. Nieszczelności mogą występować w miejscach połączeń, uszczelnień czy zaworów, dlatego regularne kontrole i konserwacja są kluczowe dla zapewnienia prawidłowego funkcjonowania systemu. Kolejnym istotnym zagadnieniem jest zanieczyszczenie powietrza, które może wpłynąć na działanie siłowników oraz innych komponentów. Zanieczyszczenia mogą powodować zużycie elementów mechanicznych, a także prowadzić do awarii całego układu. Warto również zwrócić uwagę na problemy związane z niewłaściwym doborem komponentów, co może skutkować nieefektywnym działaniem maszyny lub jej uszkodzeniem. Często zdarza się również, że operatorzy nie przestrzegają zasad obsługi maszyn pneumatycznych, co prowadzi do ich niewłaściwego użytkowania i przyspieszonego zużycia. Dlatego tak ważne jest szkolenie pracowników oraz stosowanie się do zaleceń producentów dotyczących eksploatacji i konserwacji urządzeń.
Jakie są różnice między maszynami pneumatycznymi a hydraulicznymi
Maszyny pneumatyczne i hydrauliczne to dwa różne systemy napędowe, które mają swoje unikalne cechy oraz zastosowania. Główna różnica między nimi polega na medium roboczym – maszyny pneumatyczne wykorzystują sprężone powietrze, podczas gdy maszyny hydrauliczne operują cieczą pod ciśnieniem. Dzięki temu maszyny pneumatyczne są lżejsze i bardziej mobilne, co czyni je idealnymi do zastosowań w miejscach o ograniczonej przestrzeni. Z drugiej strony maszyny hydrauliczne charakteryzują się większą siłą i momentem obrotowym, co sprawia, że są bardziej odpowiednie do zadań wymagających dużej mocy. W kontekście kosztów eksploatacyjnych maszyny pneumatyczne zazwyczaj generują niższe koszty utrzymania ze względu na prostszą budowę oraz mniejsze ryzyko wycieków płynów roboczych. Jednakże w przypadku maszyn hydraulicznych możliwe jest osiągnięcie wyższej precyzji oraz stabilności pracy przy dużych obciążeniach. Wybór między tymi dwoma systemami zależy od specyfiki danego zadania oraz wymagań aplikacji.
Jakie są kluczowe czynniki wpływające na efektywność maszyn pneumatycznych
Efektywność maszyn pneumatycznych zależy od wielu czynników, które mogą wpływać na ich wydajność oraz niezawodność. Przede wszystkim istotne jest odpowiednie dobranie komponentów układu pneumatycznego, takich jak sprężarki, zawory czy siłowniki. Każdy z tych elementów powinien być dostosowany do specyfiki aplikacji oraz wymagań produkcyjnych. Kolejnym czynnikiem jest jakość sprężonego powietrza – jego czystość oraz poziom wilgotności mają kluczowe znaczenie dla prawidłowego funkcjonowania maszyn. Zanieczyszczone lub wilgotne powietrze może prowadzić do uszkodzeń komponentów oraz obniżenia efektywności działania układu. Również regularna konserwacja i serwisowanie maszyn mają ogromny wpływ na ich wydajność – zaniedbanie tych czynności może skutkować zwiększoną awaryjnością oraz kosztami napraw. Ważnym aspektem jest także szkolenie operatorów – dobrze przeszkolony personel potrafi efektywnie obsługiwać maszyny oraz minimalizować ryzyko błędów podczas pracy. Ostatecznie warto zwrócić uwagę na optymalizację procesów produkcyjnych poprzez analizę danych dotyczących wydajności maszyn oraz wprowadzenie ewentualnych usprawnień w organizacji pracy.
Jakie są przyszłościowe kierunki rozwoju technologii pneumatycznej
Przyszłość technologii pneumatycznej zapowiada się bardzo obiecująco dzięki ciągłemu rozwojowi innowacyjnych rozwiązań oraz rosnącemu zapotrzebowaniu na automatyzację procesów przemysłowych. Jednym z kluczowych kierunków rozwoju jest integracja technologii Internetu Rzeczy (IoT) z systemami pneumatycznymi, co pozwoli na zbieranie danych w czasie rzeczywistym oraz monitorowanie stanu technicznego maszyn. Dzięki temu możliwe będzie szybsze wykrywanie usterek oraz optymalizacja procesów serwisowych, co przyczyni się do zwiększenia efektywności działania całego układu. Również rozwój sztucznej inteligencji otwiera nowe możliwości w zakresie analizy danych oraz podejmowania decyzji w czasie rzeczywistym, co może znacząco wpłynąć na poprawę wydajności produkcji. Innowacje w zakresie materiałów konstrukcyjnych pozwalają na tworzenie lżejszych i bardziej wytrzymałych komponentów, co przekłada się na większą elastyczność oraz mobilność maszyn pneumatycznych. Ponadto rosnąca świadomość ekologiczna skłania producentów do opracowywania rozwiązań minimalizujących zużycie energii oraz emisję hałasu podczas pracy urządzeń pneumatycznych.
Jakie są kluczowe aspekty bezpieczeństwa przy pracy z maszynami pneumatycznymi
Bezpieczeństwo pracy z maszynami pneumatycznymi jest niezwykle istotnym zagadnieniem, które należy uwzględnić na każdym etapie eksploatacji tych urządzeń. Przede wszystkim ważne jest przestrzeganie zasad BHP oraz stosowanie odpowiednich środków ochrony osobistej przez operatorów maszyn. Należy zapewnić pracownikom dostęp do kasków ochronnych, rękawic czy okularów ochronnych, aby zminimalizować ryzyko urazów podczas pracy z urządzeniami pneumatycznymi. Kluczowym aspektem bezpieczeństwa jest również regularna konserwacja i kontrola stanu technicznego maszyn – wszelkie nieszczelności czy uszkodzenia powinny być niezwłocznie naprawiane, aby uniknąć potencjalnych awarii czy wypadków. Operatorzy powinni być odpowiednio przeszkoleni w zakresie obsługi urządzeń pneumatycznych oraz znajomości procedur awaryjnych, aby mogli szybko reagować w sytuacjach kryzysowych. Ważne jest także stosowanie zabezpieczeń mechanicznych takich jak osłony czy blokady, które uniemożliwią przypadkowy dostęp do ruchomych części maszyny podczas jej pracy lub konserwacji.