Fabryka przyszłości 4.0 to koncepcja, która odnosi się do nowoczesnych procesów produkcyjnych, które wykorzystują zaawansowane technologie, takie jak Internet rzeczy, sztuczna inteligencja oraz automatyzacja. W erze przemysłu 4.0, zakłady produkcyjne stają się bardziej zintegrowane i elastyczne, co pozwala na szybsze dostosowanie się do zmieniających się potrzeb rynku. W fabrykach przyszłości kluczową rolę odgrywają dane, które są zbierane w czasie rzeczywistym i analizowane w celu optymalizacji procesów produkcyjnych. Dzięki zastosowaniu czujników i urządzeń IoT, maszyny mogą komunikować się ze sobą oraz z systemami zarządzania, co prowadzi do zwiększenia efektywności operacyjnej. Wprowadzenie robotów i automatyzacji pozwala na redukcję kosztów pracy oraz minimalizację błędów ludzkich. Fabryki przyszłości są również bardziej zrównoważone ekologicznie, dzięki zastosowaniu technologii umożliwiających oszczędność energii oraz redukcję odpadów.
Jakie technologie wspierają rozwój fabryk przyszłości 4.0
W rozwoju fabryk przyszłości 4.0 kluczowe znaczenie mają różnorodne technologie, które wspierają automatyzację i cyfryzację procesów produkcyjnych. Jedną z najważniejszych technologii jest Internet rzeczy, który pozwala na połączenie maszyn i urządzeń w sieć, umożliwiając im wymianę danych w czasie rzeczywistym. Dzięki temu możliwe jest monitorowanie stanu maszyn oraz przewidywanie awarii zanim one nastąpią, co znacząco zwiększa efektywność produkcji. Kolejną istotną technologią jest sztuczna inteligencja, która pozwala na analizę dużych zbiorów danych oraz podejmowanie decyzji na podstawie algorytmów uczenia maszynowego. Automatyzacja procesów produkcyjnych za pomocą robotów przemysłowych również odgrywa kluczową rolę w fabrykach przyszłości, ponieważ pozwala na zwiększenie wydajności oraz precyzji wykonywanych zadań. Dodatkowo technologie takie jak wirtualna i rozszerzona rzeczywistość mogą być wykorzystywane do szkolenia pracowników oraz wizualizacji procesów produkcyjnych, co ułatwia ich zrozumienie i optymalizację.
Jakie korzyści przynosi wdrożenie fabryk przyszłości 4.0
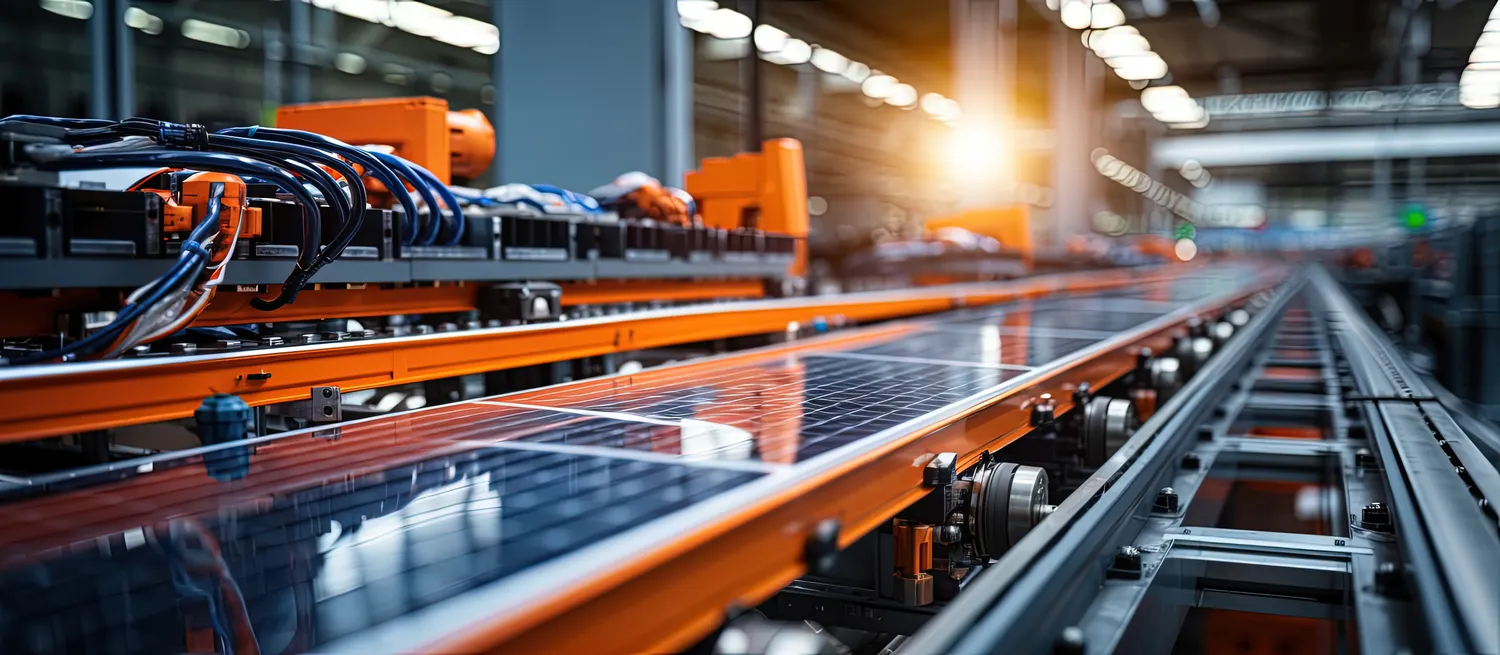
Wdrożenie koncepcji fabryk przyszłości 4.0 niesie ze sobą szereg korzyści dla przedsiębiorstw oraz ich pracowników. Przede wszystkim zwiększa efektywność produkcji poprzez automatyzację wielu procesów, co prowadzi do obniżenia kosztów operacyjnych. Dzięki zastosowaniu nowoczesnych technologii możliwe jest szybsze wprowadzanie nowych produktów na rynek oraz lepsze dostosowanie oferty do potrzeb klientów. Fabryki przyszłości charakteryzują się także większą elastycznością, co pozwala na łatwiejsze dostosowywanie linii produkcyjnych do zmieniających się wymagań rynkowych. Kolejną istotną korzyścią jest poprawa jakości produktów dzięki zastosowaniu zaawansowanych systemów monitorowania i kontroli jakości w czasie rzeczywistym. Pracownicy również korzystają na wdrożeniu tych technologii, ponieważ ich praca staje się mniej monotonna i bardziej kreatywna, a także mają możliwość rozwijania swoich umiejętności w zakresie obsługi nowoczesnych narzędzi i systemów informatycznych.
Jakie wyzwania stoją przed fabrykami przyszłości 4.0
Mimo licznych korzyści związanych z wdrożeniem koncepcji fabryk przyszłości 4.0 istnieje wiele wyzwań, które przedsiębiorstwa muszą pokonać, aby skutecznie przejść przez ten proces transformacji. Jednym z głównych problemów jest konieczność inwestycji w nowoczesne technologie oraz infrastrukturę IT, co może wiązać się z wysokimi kosztami początkowymi. Ponadto wiele firm boryka się z brakiem odpowiednich kompetencji wśród pracowników, co utrudnia wdrażanie nowych rozwiązań technologicznych. Konieczne jest więc zapewnienie odpowiednich szkoleń oraz programów edukacyjnych dla personelu, aby mogli oni skutecznie obsługiwać nowe systemy i maszyny. Innym wyzwaniem jest kwestia bezpieczeństwa danych oraz ochrona przed cyberatakami, które mogą stanowić poważne zagrożenie dla funkcjonowania zautomatyzowanych zakładów produkcyjnych.
Jakie przykłady fabryk przyszłości 4.0 można znaleźć na świecie
Na świecie istnieje wiele przykładów fabryk przyszłości 4.0, które skutecznie wdrożyły nowoczesne technologie i zrewolucjonizowały swoje procesy produkcyjne. Jednym z najbardziej znanych przykładów jest fabryka BMW w Lipsku, która wykorzystuje zaawansowane systemy automatyzacji oraz roboty do produkcji samochodów. Dzięki zastosowaniu technologii IoT, maszyny w tej fabryce są w stanie komunikować się ze sobą oraz z centralnym systemem zarządzania, co pozwala na optymalizację procesów produkcyjnych i zwiększenie wydajności. Innym interesującym przypadkiem jest fabryka Siemens w Amberg, która stała się wzorem dla przemysłu 4.0 dzięki zastosowaniu inteligentnych systemów produkcyjnych oraz analizy danych w czasie rzeczywistym. W tej fabryce każdy produkt jest monitorowany na każdym etapie produkcji, co pozwala na szybkie wykrywanie błędów i ich eliminację. Warto również wspomnieć o firmie Foxconn, która produkuje urządzenia elektroniczne dla takich gigantów jak Apple czy Sony. W swoich zakładach Foxconn wdraża nowoczesne technologie automatyzacji oraz sztucznej inteligencji, co pozwala na zwiększenie efektywności produkcji oraz redukcję kosztów.
Jakie umiejętności będą potrzebne w fabrykach przyszłości 4.0
W miarę jak fabryki przyszłości 4.0 stają się coraz bardziej zautomatyzowane i cyfrowe, rośnie zapotrzebowanie na pracowników posiadających odpowiednie umiejętności techniczne oraz analityczne. Kluczowe znaczenie mają kompetencje związane z obsługą nowoczesnych technologii, takich jak robotyka, sztuczna inteligencja czy Internet rzeczy. Pracownicy muszą być w stanie nie tylko obsługiwać te systemy, ale także analizować dane generowane przez maszyny i podejmować decyzje na ich podstawie. Umiejętności programowania stają się coraz bardziej pożądane, ponieważ wiele procesów produkcyjnych opiera się na oprogramowaniu i algorytmach. Ponadto ważne jest rozwijanie zdolności interpersonalnych, takich jak umiejętność pracy w zespole oraz komunikacji, ponieważ współpraca między ludźmi a maszynami będzie kluczowa w nowoczesnym środowisku pracy. Pracownicy powinni również być otwarci na ciągłe uczenie się i doskonalenie swoich umiejętności, aby nadążyć za dynamicznymi zmianami w technologii i wymaganiami rynku.
Jakie są perspektywy rozwoju fabryk przyszłości 4.0
Perspektywy rozwoju fabryk przyszłości 4.0 są niezwykle obiecujące, a wiele prognoz wskazuje na dalszy wzrost znaczenia technologii cyfrowych w przemyśle. W miarę jak technologia będzie się rozwijać, możemy spodziewać się jeszcze większej automatyzacji procesów produkcyjnych oraz integracji różnych systemów informatycznych. Przemysł 4.0 ma potencjał do stworzenia bardziej elastycznych i responsywnych linii produkcyjnych, które będą mogły szybko dostosowywać się do zmieniających się potrzeb klientów oraz warunków rynkowych. Wzrost znaczenia zrównoważonego rozwoju sprawi również, że przedsiębiorstwa będą musiały inwestować w technologie pozwalające na oszczędność energii i minimalizację odpadów. Dodatkowo rozwój sztucznej inteligencji i uczenia maszynowego otworzy nowe możliwości analizy danych oraz optymalizacji procesów produkcyjnych. Możemy również spodziewać się większej liczby innowacji w zakresie materiałów i technologii produkcji, co przyczyni się do dalszego zwiększenia konkurencyjności firm na rynku globalnym.
Jakie zmiany społeczne wiążą się z fabrykami przyszłości 4.0
Wprowadzenie koncepcji fabryk przyszłości 4.0 wiąże się nie tylko z technologicznymi innowacjami, ale także z istotnymi zmianami społecznymi, które mogą wpłynąć na rynek pracy oraz życie codzienne ludzi. Automatyzacja procesów produkcyjnych może prowadzić do redukcji miejsc pracy w tradycyjnych sektorach przemysłu, co stanowi wyzwanie dla pracowników o niskich kwalifikacjach. Z drugiej strony pojawią się nowe miejsca pracy związane z obsługą nowoczesnych technologii oraz zarządzaniem danymi, co wymaga odpowiednich umiejętności technicznych i analitycznych. W związku z tym konieczne będzie dostosowanie systemu edukacji do zmieniających się potrzeb rynku pracy oraz zapewnienie programów przekwalifikowania dla osób dotkniętych zmianami strukturalnymi w gospodarce. Ponadto rozwój fabryk przyszłości może przyczynić się do poprawy jakości życia poprzez zwiększenie wydajności produkcji oraz dostępność produktów wysokiej jakości po niższych cenach.
Jakie są kluczowe trendy w rozwoju fabryk przyszłości 4.0
Rozwój fabryk przyszłości 4.0 wiąże się z wieloma kluczowymi trendami, które kształtują sposób funkcjonowania przemysłu na całym świecie. Jednym z najważniejszych trendów jest rosnąca automatyzacja procesów produkcyjnych, która pozwala na zwiększenie wydajności oraz redukcję kosztów operacyjnych. Zastosowanie robotyzacji i sztucznej inteligencji umożliwia przedsiębiorstwom szybsze reagowanie na zmieniające się potrzeby rynku oraz poprawę jakości produktów poprzez eliminację błędów ludzkich. Kolejnym istotnym trendem jest digitalizacja procesów biznesowych, która pozwala na zbieranie i analizowanie danych w czasie rzeczywistym, co prowadzi do lepszej optymalizacji procesów produkcyjnych oraz podejmowania bardziej świadomych decyzji zarządczych. Wzrasta również znaczenie zrównoważonego rozwoju i ekologicznych praktyk w przemyśle, co skłania firmy do inwestowania w technologie umożliwiające oszczędność energii oraz redukcję odpadów. Dodatkowo rośnie zainteresowanie personalizacją produktów i usług, co wymaga elastycznych linii produkcyjnych zdolnych do szybkiego dostosowywania oferty do indywidualnych potrzeb klientów.
Jakie są największe wyzwania związane z transformacją ku fabrykom przyszłości 4.0
Transformacja ku fabrykom przyszłości 4.0 wiąże się z wieloma wyzwaniami, które przedsiębiorstwa muszą pokonać, aby skutecznie wdrożyć nowoczesne technologie i osiągnąć zamierzone cele biznesowe. Jednym z głównych wyzwań jest konieczność przeprowadzenia gruntownej analizy obecnych procesów produkcyjnych oraz identyfikacji obszarów wymagających poprawy lub modernizacji. Firmy często borykają się również z problemem braku odpowiednich zasobów finansowych na inwestycje w nowe technologie oraz infrastrukturę IT, co może spowolnić proces transformacji. Kolejnym istotnym wyzwaniem jest brak kompetencji technicznych wśród pracowników oraz trudności związane z przekwalifikowaniem personelu do obsługi nowoczesnych narzędzi i systemów informatycznych. Bez odpowiednich szkoleń i wsparcia ze strony kierownictwa wdrożenie nowych rozwiązań może okazać się nieefektywne lub wręcz niemożliwe do realizacji.