Destylator przemysłowy to zaawansowane urządzenie wykorzystywane do separacji składników cieczy na podstawie różnic w ich temperaturach wrzenia. Proces ten jest kluczowy w wielu branżach, takich jak chemiczna, petrochemiczna czy spożywcza. Działanie destylatora opiera się na cyklu podgrzewania cieczy, co powoduje jej parowanie, a następnie skraplanie pary w osobnej komorze. W wyniku tego procesu uzyskuje się czystsze frakcje substancji, które można dalej przetwarzać lub wykorzystywać w produkcji. Destylatory przemysłowe mogą mieć różne formy, od prostych kolumn destylacyjnych po bardziej skomplikowane systemy z wieloma poziomami separacji. W zależności od zastosowania, destylatory mogą być dostosowane do pracy z różnymi rodzajami cieczy, co czyni je niezwykle wszechstronnymi narzędziami w przemyśle.
Jakie są zastosowania destylatorów przemysłowych w różnych branżach
Destylatory przemysłowe znajdują szerokie zastosowanie w wielu sektorach gospodarki, co czyni je niezbędnym elementem nowoczesnej produkcji. W przemyśle chemicznym służą do oczyszczania surowców oraz produkcji różnych substancji chemicznych, takich jak rozpuszczalniki czy kwasy. W branży petrochemicznej destylacja jest kluczowym procesem przy produkcji paliw, gdzie surowa ropa naftowa jest poddawana destylacji frakcyjnej w celu uzyskania benzyny, oleju napędowego i innych produktów naftowych. W przemyśle spożywczym destylatory są wykorzystywane do produkcji alkoholi oraz ekstraktów smakowych. Na przykład, w produkcji whisky czy wina proces destylacji pozwala na uzyskanie pożądanych aromatów i smaków. Ponadto, destylatory znajdują zastosowanie w laboratoriach badawczych do analizy substancji chemicznych oraz ich oczyszczania.
Jakie są różnice między destylatorami przemysłowymi a laboratoryjnymi
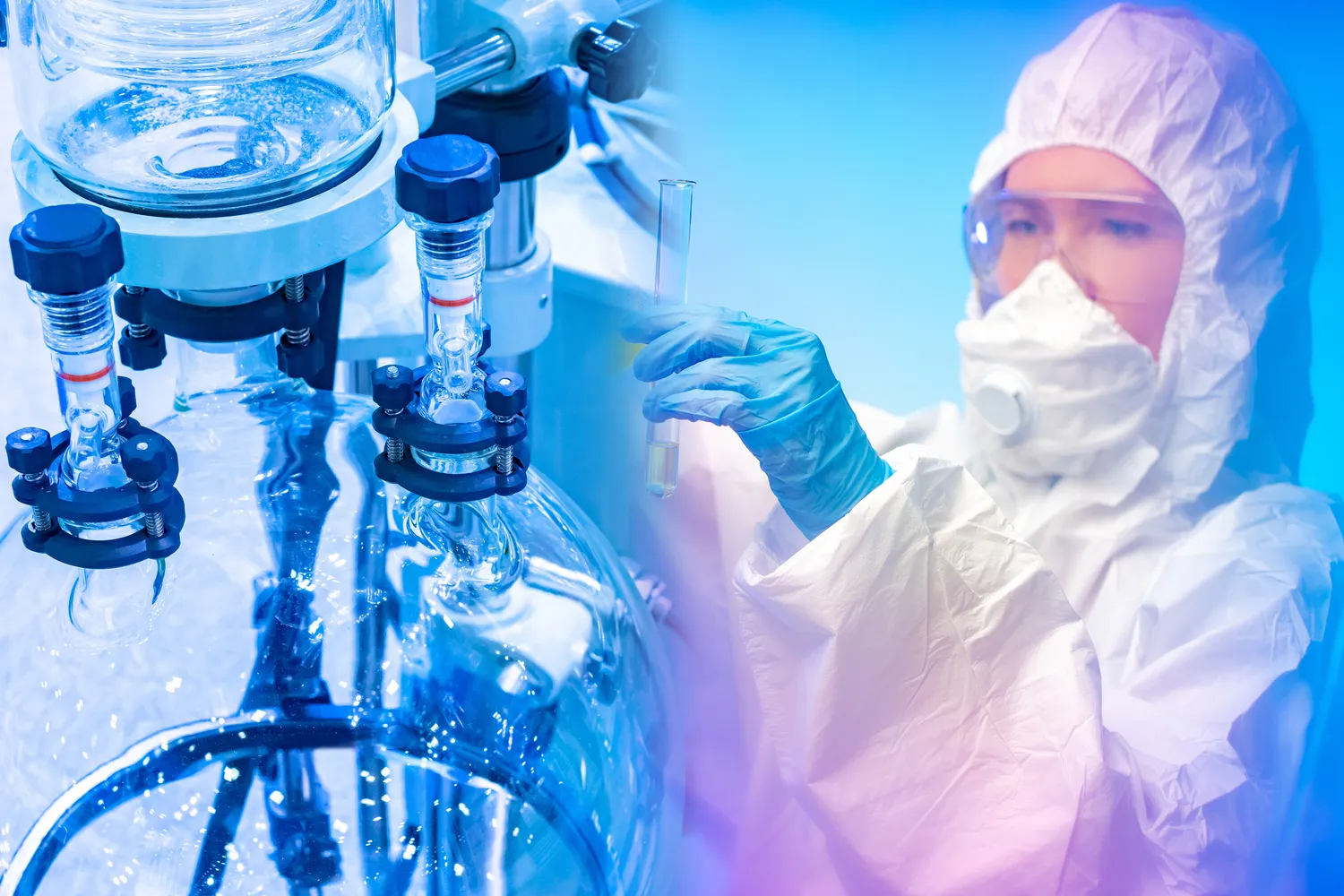
Różnice między destylatorami przemysłowymi a laboratoryjnymi są znaczące i wynikają głównie z ich przeznaczenia oraz skali działania. Destylatory przemysłowe są zaprojektowane do pracy na dużą skalę, co oznacza, że mogą przetwarzać znaczne ilości cieczy w krótkim czasie. Zazwyczaj charakteryzują się one bardziej zaawansowanymi systemami automatyzacji oraz kontrolą procesów, co pozwala na optymalizację wydajności i jakości produktów końcowych. Z kolei destylatory laboratoryjne są zazwyczaj mniejsze i służą do przeprowadzania eksperymentów oraz badań naukowych. Ich konstrukcja umożliwia łatwiejszą manipulację oraz mniejsze objętości próbek. W laboratoriach często stosuje się prostsze modele destylatorów, takie jak kolumny szklane czy aparaty do destylacji prostej. Różnice te wpływają również na koszty eksploatacji oraz wymagania dotyczące konserwacji urządzeń.
Jakie są najnowsze technologie stosowane w destylatorach przemysłowych
W ostatnich latach rozwój technologii wpłynął znacząco na efektywność i wydajność destylatorów przemysłowych. Nowoczesne rozwiązania obejmują zastosowanie materiałów o wysokiej przewodności cieplnej oraz innowacyjnych konstrukcji kolumn destylacyjnych, co pozwala na szybsze osiąganie wymaganych temperatur i lepszą separację składników. Wprowadzenie automatyzacji do procesów destylacyjnych umożliwia zdalne monitorowanie i kontrolę parametrów pracy urządzenia, co zwiększa bezpieczeństwo oraz redukuje ryzyko błędów ludzkich. Ponadto coraz częściej stosuje się technologie odzysku ciepła, które pozwalają na zmniejszenie zużycia energii podczas procesu destylacji. Innowacyjne podejścia obejmują także wykorzystanie sztucznej inteligencji do optymalizacji procesów produkcyjnych oraz analizy danych operacyjnych w czasie rzeczywistym. Dzięki tym technologiom możliwe jest nie tylko zwiększenie wydajności produkcji, ale także poprawa jakości uzyskiwanych produktów końcowych.
Jakie są kluczowe elementy konstrukcyjne destylatorów przemysłowych
Kluczowe elementy konstrukcyjne destylatorów przemysłowych mają ogromne znaczenie dla efektywności i wydajności procesu destylacji. Podstawowym komponentem jest kolumna destylacyjna, która może mieć różne formy, w zależności od zastosowania. W kolumnach frakcyjnych stosuje się różnego rodzaju wypełnienia, które zwiększają powierzchnię kontaktu między parą a cieczą, co pozwala na lepszą separację składników. Innym istotnym elementem jest zbiornik do kondensacji, który umożliwia skraplanie pary i zbieranie uzyskanych frakcji. Wysokiej jakości wymienniki ciepła są również niezbędne do efektywnego podgrzewania cieczy oraz odzyskiwania ciepła z procesu. Dodatkowo, systemy pomiarowe i kontrolne są kluczowe dla monitorowania parametrów pracy destylatora, takich jak temperatura, ciśnienie czy przepływ. W nowoczesnych destylatorach często stosuje się automatyczne systemy sterowania, które pozwalają na optymalizację procesów oraz minimalizację ryzyka awarii.
Jakie są koszty eksploatacji destylatorów przemysłowych
Koszty eksploatacji destylatorów przemysłowych mogą być znaczne i zależą od wielu czynników, takich jak rodzaj przetwarzanej cieczy, skala produkcji oraz zastosowane technologie. Jednym z głównych kosztów jest zużycie energii, które może stanowić znaczną część całkowitych wydatków operacyjnych. W przypadku dużych instalacji przemysłowych warto inwestować w technologie odzysku ciepła oraz automatyzację procesów, co pozwala na obniżenie kosztów energetycznych. Kolejnym istotnym czynnikiem są koszty konserwacji i utrzymania urządzeń w dobrym stanie technicznym. Regularne przeglądy oraz wymiana zużytych części są niezbędne dla zapewnienia ciągłości produkcji oraz uniknięcia awarii. Koszty surowców również mają duże znaczenie, zwłaszcza w branżach, gdzie ceny materiałów mogą być zmienne. Dodatkowo, należy uwzględnić koszty związane z przestrzeganiem norm środowiskowych oraz bezpieczeństwa pracy, co może wiązać się z koniecznością inwestycji w odpowiednie systemy filtracyjne czy zabezpieczenia przeciwpożarowe.
Jakie są najczęstsze problemy związane z użytkowaniem destylatorów przemysłowych
Użytkowanie destylatorów przemysłowych wiąże się z wieloma wyzwaniami i problemami, które mogą wpływać na efektywność procesu produkcyjnego. Jednym z najczęstszych problemów jest osadzanie się zanieczyszczeń na ściankach kolumny destylacyjnej, co prowadzi do obniżenia wydajności separacji składników. Regularne czyszczenie i konserwacja urządzeń są kluczowe dla utrzymania ich sprawności. Innym istotnym zagadnieniem jest kontrola temperatury i ciśnienia wewnątrz systemu; niewłaściwe ustawienia mogą prowadzić do nieefektywnej destylacji lub nawet uszkodzenia sprzętu. Problemy z układami chłodzenia mogą również wpłynąć na jakość uzyskiwanych frakcji, dlatego ważne jest monitorowanie tych systemów w czasie rzeczywistym. Dodatkowo, zmiany w składzie surowców mogą powodować trudności w osiągnięciu stabilnych parametrów pracy destylatora. W takich przypadkach konieczne może być dostosowanie ustawień lub modyfikacja procesu technologicznego.
Jakie są różnice między różnymi rodzajami destylatorów przemysłowych
Różnorodność rodzajów destylatorów przemysłowych wynika z różnych potrzeb technologicznych oraz specyfiki przetwarzanych substancji. Najpopularniejszym typem jest kolumna destylacyjna, która umożliwia separację składników na podstawie różnic w temperaturze wrzenia przy wykorzystaniu wielokrotnego skraplania i parowania. Istnieją także destylatory prostsze, takie jak aparaty do destylacji prostej, które znajdują zastosowanie w laboratoriach oraz małych zakładach produkcyjnych. Inny rodzaj to destylatory próżniowe, które działają w obniżonym ciśnieniu; dzięki temu możliwe jest przeprowadzanie procesów w niższych temperaturach, co minimalizuje ryzyko degradacji termicznej delikatnych substancji. Destylatory azeotropowe są jeszcze innym przykładem; stosuje się je do separacji mieszanin tworzących azeotropy, gdzie tradycyjne metody mogą być nieskuteczne.
Jakie są przyszłe kierunki rozwoju technologii destylacyjnej
Przyszłość technologii destylacyjnej zapowiada się obiecująco dzięki ciągłemu rozwojowi innowacyjnych rozwiązań inżynieryjnych oraz rosnącej świadomości ekologicznej w przemyśle. Jednym z kluczowych kierunków rozwoju jest zwiększenie efektywności energetycznej procesów destylacyjnych poprzez zastosowanie zaawansowanych systemów odzysku ciepła oraz alternatywnych źródeł energii odnawialnej. Technologia cyfrowa również odgrywa coraz większą rolę; automatyzacja procesów oraz wykorzystanie sztucznej inteligencji do analizy danych operacyjnych pozwalają na optymalizację pracy urządzeń oraz szybsze reagowanie na zmiany warunków pracy. Ponadto rozwijają się technologie związane z mikro-destylacją oraz nanotechnologią, które mogą prowadzić do bardziej precyzyjnej separacji składników przy mniejszych stratach surowców i energii. Również aspekty związane z ochroną środowiska stają się coraz ważniejsze; rozwój biotechnologii może przyczynić się do opracowania bardziej ekologicznych metod separacji substancji chemicznych bez użycia szkodliwych rozpuszczalników czy chemikaliów.
Jakie są wymagania dotyczące bezpieczeństwa przy użytkowaniu destylatorów przemysłowych
Bezpieczeństwo użytkowania destylatorów przemysłowych jest kluczowym zagadnieniem zarówno dla pracowników, jak i dla ochrony środowiska. Przemysłowe procesy destylacyjne często wiążą się z pracą z substancjami chemicznymi o wysokiej toksyczności lub łatwopalności, dlatego konieczne jest przestrzeganie rygorystycznych norm bezpieczeństwa. Pracownicy powinni być odpowiednio przeszkoleni w zakresie obsługi urządzeń oraz procedur awaryjnych; regularne szkolenia pomagają utrzymać wysoki poziom świadomości dotyczącej potencjalnych zagrożeń. Ważnym aspektem jest także stosowanie odpowiednich środków ochrony osobistej, takich jak odzież ochronna czy sprzęt zabezpieczający oczy i drogi oddechowe. Systemy wentylacyjne powinny być dostosowane do specyfiki procesu produkcyjnego; zapewnienie odpowiedniej wymiany powietrza minimalizuje ryzyko gromadzenia się szkodliwych oparów czy gazów. Dodatkowo instalacje muszą być regularnie kontrolowane pod kątem ewentualnych wycieków czy uszkodzeń; wszelkie nieprawidłowości powinny być natychmiast zgłaszane i usuwane przez wykwalifikowany personel techniczny.