Przemysł 4.0 to termin, który odnosi się do czwartej rewolucji przemysłowej, która charakteryzuje się zastosowaniem nowoczesnych technologii w procesach produkcyjnych. W odróżnieniu od wcześniejszych rewolucji, które koncentrowały się na mechanizacji i automatyzacji, przemysł 4.0 wprowadza inteligentne systemy, które potrafią komunikować się ze sobą oraz analizować dane w czasie rzeczywistym. Kluczowym elementem tego zjawiska jest Internet Rzeczy (IoT), który umożliwia połączenie maszyn, urządzeń i ludzi w jedną sieć. Dzięki temu przedsiębiorstwa mogą optymalizować swoje procesy produkcyjne, zwiększać efektywność oraz obniżać koszty. Przemysł 4.0 nie tylko zmienia sposób produkcji, ale także wpływa na organizację pracy i relacje między pracownikami a technologią.
Jakie technologie są kluczowe dla przemysłu 4.0?
W kontekście przemysłu 4.0 istnieje wiele technologii, które odgrywają kluczową rolę w transformacji procesów produkcyjnych. Przede wszystkim warto zwrócić uwagę na sztuczną inteligencję (AI), która pozwala na analizowanie ogromnych zbiorów danych oraz podejmowanie decyzji w oparciu o te analizy. Kolejną istotną technologią jest robotyzacja, która umożliwia automatyzację wielu zadań oraz zwiększa precyzję i szybkość produkcji. Warto również wspomnieć o druku 3D, który rewolucjonizuje sposób wytwarzania produktów poprzez umożliwienie ich tworzenia na żądanie i z mniejszych ilości materiałów. Technologie chmurowe również mają ogromne znaczenie, ponieważ pozwalają na przechowywanie danych oraz ich łatwy dostęp z różnych lokalizacji. Zastosowanie systemów cyber-fizycznych sprawia, że maszyny mogą monitorować swoje własne działanie i dostosowywać je do zmieniających się warunków.
Jakie korzyści przynosi wdrożenie przemysłu 4.0?
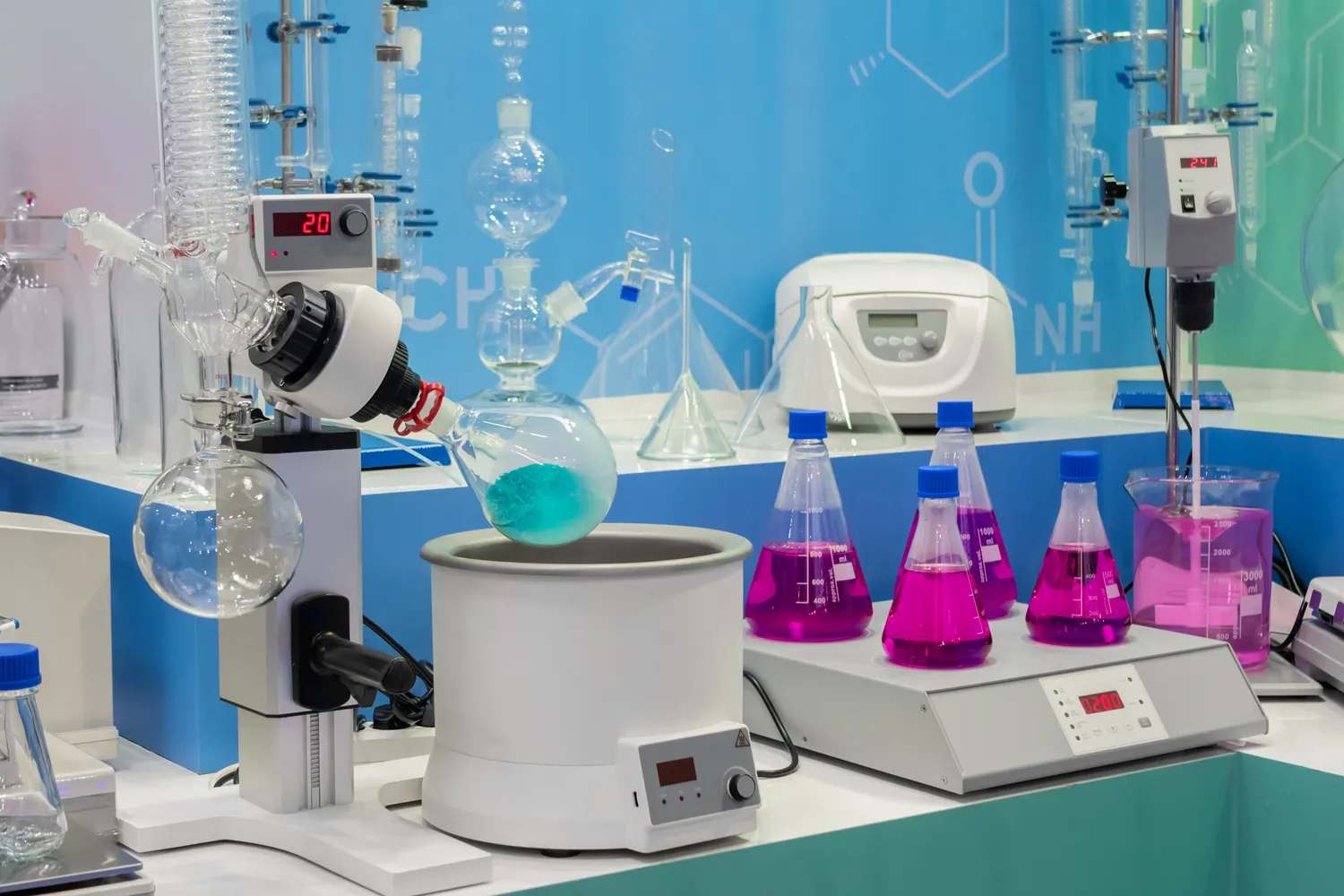
Wdrożenie przemysłu 4.0 przynosi wiele korzyści zarówno dla przedsiębiorstw, jak i dla całej gospodarki. Po pierwsze, dzięki zastosowaniu nowoczesnych technologii firmy mogą znacznie zwiększyć swoją wydajność produkcyjną. Automatyzacja procesów pozwala na szybsze wykonywanie zadań oraz redukcję błędów ludzkich, co przekłada się na wyższą jakość produktów. Po drugie, przedsiębiorstwa są w stanie lepiej reagować na zmieniające się potrzeby klientów dzięki elastyczności oferowanej przez inteligentne systemy zarządzania produkcją. Możliwość personalizacji produktów staje się standardem w wielu branżach, co zwiększa satysfakcję klientów i lojalność wobec marki. Dodatkowo wdrożenie rozwiązań związanych z danymi pozwala na lepsze prognozowanie popytu oraz optymalizację zapasów, co prowadzi do oszczędności finansowych.
Jakie wyzwania wiążą się z przemysłem 4.0?
Mimo licznych korzyści związanych z wdrożeniem przemysłu 4.0 istnieje także szereg wyzwań, które przedsiębiorstwa muszą pokonać podczas tej transformacji. Jednym z głównych problemów jest konieczność inwestycji w nowoczesne technologie oraz infrastrukturę IT, co może być kosztowne dla wielu firm, szczególnie tych mniejszych lub średnich. Ponadto pojawia się potrzeba przeszkolenia pracowników w zakresie obsługi nowych systemów oraz technologii, co wymaga czasu i zasobów ludzkich. Kolejnym wyzwaniem jest kwestia bezpieczeństwa danych – wraz z rosnącą ilością połączonych urządzeń wzrasta ryzyko cyberataków oraz kradzieży danych. Firmy muszą więc inwestować w zabezpieczenia oraz rozwijać polityki ochrony informacji. Również integracja różnych systemów i technologii może być skomplikowana i czasochłonna, co może opóźnić pełne wdrożenie rozwiązań związanych z przemysłem 4.0.
Jakie są przykłady zastosowania przemysłu 4.0 w praktyce?
Przemysł 4.0 znajduje zastosowanie w wielu branżach, co ilustruje jego wszechstronność oraz potencjał do transformacji tradycyjnych procesów produkcyjnych. W sektorze motoryzacyjnym wiele firm wdraża zautomatyzowane linie produkcyjne, które wykorzystują roboty do montażu pojazdów. Dzięki temu możliwe jest zwiększenie wydajności oraz redukcja błędów, co przekłada się na wyższą jakość końcowego produktu. W branży spożywczej zastosowanie technologii IoT pozwala na monitorowanie warunków przechowywania żywności, co zwiększa bezpieczeństwo produktów i minimalizuje straty. Przykładem może być inteligentne zarządzanie magazynem, gdzie czujniki monitorują temperaturę i wilgotność, a systemy informatyczne automatycznie dostosowują warunki przechowywania. W sektorze energetycznym przemysł 4.0 przyczynia się do rozwoju inteligentnych sieci energetycznych, które umożliwiają efektywne zarządzanie dostawami energii oraz integrację odnawialnych źródeł energii. Zastosowanie analityki danych pozwala na przewidywanie awarii oraz optymalizację zużycia energii, co przyczynia się do zrównoważonego rozwoju.
Jakie umiejętności są potrzebne w erze przemysłu 4.0?
W erze przemysłu 4.0 zmieniają się wymagania dotyczące umiejętności pracowników, co stawia przed nimi nowe wyzwania. Kluczowe stają się kompetencje związane z obsługą nowoczesnych technologii, takich jak programowanie czy analiza danych. Pracownicy muszą być w stanie korzystać z systemów informatycznych oraz narzędzi analitycznych, aby efektywnie wykonywać swoje zadania. Również umiejętności związane z robotyką i automatyzacją stają się coraz bardziej pożądane na rynku pracy. Warto również zwrócić uwagę na znaczenie umiejętności miękkich, takich jak zdolność do pracy w zespole oraz komunikacji między działami. Współpraca między specjalistami z różnych dziedzin jest kluczowa dla skutecznego wdrażania rozwiązań przemysłu 4.0. Ponadto elastyczność oraz otwartość na zmiany są niezbędne w dynamicznie rozwijającym się środowisku technologicznym.
Jakie są przyszłe kierunki rozwoju przemysłu 4.0?
Przemysł 4.0 to dynamicznie rozwijający się obszar, który będzie ewoluował w nadchodzących latach w odpowiedzi na zmieniające się potrzeby rynku oraz postęp technologiczny. Jednym z kluczowych kierunków rozwoju jest dalsza integracja sztucznej inteligencji w procesach produkcyjnych, co pozwoli na jeszcze większą automatyzację oraz optymalizację działań przedsiębiorstw. Rozwój technologii chmurowych również będzie miał istotny wpływ na sposób zarządzania danymi oraz ich analizę, co umożliwi lepsze prognozowanie popytu i planowanie produkcji. Kolejnym ważnym aspektem jest rosnąca rola zrównoważonego rozwoju – przedsiębiorstwa będą coraz częściej poszukiwać sposobów na minimalizację swojego wpływu na środowisko poprzez efektywne wykorzystanie zasobów oraz ograniczenie odpadów. Warto również zwrócić uwagę na rozwój technologii blockchain, która może przyczynić się do zwiększenia transparentności procesów produkcyjnych oraz poprawy bezpieczeństwa danych.
Jakie są różnice między przemysłem 4.0 a wcześniejszymi rewolucjami przemysłowymi?
Przemysł 4.0 różni się od wcześniejszych rewolucji przemysłowych pod wieloma względami, co sprawia, że jest unikalnym zjawiskiem w historii produkcji i technologii. Pierwsza rewolucja przemysłowa skupiała się głównie na mechanizacji produkcji za pomocą maszyn parowych, co znacznie zwiększyło wydajność pracy ludzkiej, ale nie zmieniło jeszcze fundamentalnie sposobu organizacji pracy czy struktury przedsiębiorstw. Druga rewolucja przyniosła elektryczność i masową produkcję, co umożliwiło dalszą automatyzację procesów oraz zwiększenie skali produkcji. Trzecia rewolucja natomiast była związana z rozwojem komputerów i technologii informacyjnej, co pozwoliło na bardziej zaawansowane zarządzanie procesami produkcyjnymi oraz wprowadzenie systemów ERP (Enterprise Resource Planning). Przemysł 4.0 natomiast łączy te wszystkie elementy i dodaje do nich nowoczesne technologie takie jak IoT, AI czy robotyzacja, które umożliwiają pełną integrację maszyn i systemów w czasie rzeczywistym oraz samodzielne podejmowanie decyzji przez maszyny na podstawie analizy danych.
Jakie są przykłady firm wdrażających rozwiązania przemysłu 4.0?
Wiele znanych firm już wdrożyło rozwiązania związane z przemysłem 4.0, co pokazuje ich zaangażowanie w innowacje i nowoczesne technologie. Na przykład Siemens jest jednym z liderów w zakresie automatyzacji i cyfryzacji procesów produkcyjnych; firma ta wykorzystuje zaawansowane technologie IoT do monitorowania swoich zakładów produkcyjnych w czasie rzeczywistym oraz optymalizacji procesów produkcyjnych dzięki analizie danych. Inny przykład to General Electric (GE), która stworzyła platformę Predix, umożliwiającą zbieranie danych z różnych urządzeń i ich analizę celem poprawy efektywności operacyjnej w przemyśle ciężkim i energetycznym. Firmy takie jak Bosch również inwestują w rozwój inteligentnych fabryk, które wykorzystują roboty współpracujące oraz systemy cyber-fizyczne do automatyzacji procesów montażowych i logistycznych. W branży motoryzacyjnej Toyota wdraża rozwiązania związane z inteligentnymi systemami zarządzania produkcją, które pozwalają na lepsze prognozowanie popytu oraz personalizację oferty dla klientów.
Jakie są najważniejsze trendy związane z przemysłem 4.0?
W miarę jak przemysł 4.0 zdobywa popularność, pojawiają się nowe trendy kształtujące jego rozwój i implementację w różnych branżach gospodarki. Jednym z najważniejszych trendów jest rosnąca automatyzacja procesów produkcyjnych poprzez zastosowanie robotyzacji oraz sztucznej inteligencji; firmy dążą do zwiększenia wydajności i redukcji kosztów operacyjnych poprzez zastępowanie ludzi maszynami tam, gdzie to możliwe. Kolejnym istotnym trendem jest rozwój Internetu Rzeczy (IoT), który umożliwia połączenie różnych urządzeń i systemów w jedną sieć; dzięki temu możliwe jest zbieranie danych o działaniu maszyn oraz ich analiza w czasie rzeczywistym, co sprzyja podejmowaniu lepszych decyzji biznesowych. Trendem zauważalnym w ostatnich latach jest także nacisk na zrównoważony rozwój; przedsiębiorstwa starają się minimalizować swój wpływ na środowisko poprzez efektywne wykorzystanie zasobów oraz ograniczenie odpadów produkcyjnych dzięki zastosowaniu nowoczesnych technologii i metodologii Lean Manufacturing czy Circular Economy.