Smarowanie narzędzi pneumatycznych jest kluczowym elementem ich konserwacji, który wpływa na ich wydajność oraz żywotność. Aby skutecznie smarować te urządzenia, należy najpierw zrozumieć, jak działają i jakie są ich specyfikacje. Narzędzia pneumatyczne wykorzystują sprężone powietrze do wykonywania różnych zadań, takich jak wkręcanie, szlifowanie czy malowanie. Właściwe smarowanie tych narzędzi zapewnia nie tylko ich płynne działanie, ale także minimalizuje ryzyko awarii. Warto zacząć od wyboru odpowiedniego smaru, który jest dostosowany do rodzaju narzędzia oraz jego zastosowania. Na rynku dostępne są różne rodzaje smarów, w tym smary silikonowe, oleje mineralne oraz specjalistyczne preparaty przeznaczone do narzędzi pneumatycznych. Kluczowe jest również regularne czyszczenie narzędzi przed nałożeniem smaru, aby usunąć wszelkie zanieczyszczenia i resztki starego smaru.
Jakie są najlepsze metody smarowania narzędzi pneumatycznych?
Wybór odpowiedniej metody smarowania narzędzi pneumatycznych ma ogromne znaczenie dla ich efektywności. Jedną z najpopularniejszych metod jest stosowanie olejów w sprayu, które można łatwo aplikować na ruchome części narzędzia. Tego rodzaju oleje często zawierają dodatki przeciwdziałające korozji oraz poprawiające właściwości smarne. Inną metodą jest użycie smarów w tubkach lub pojemnikach, które można aplikować za pomocą pistoletu smarowego. Ważne jest, aby stosować odpowiednią ilość smaru – zarówno jego nadmiar, jak i niedobór mogą prowadzić do problemów z działaniem narzędzia. Dobrą praktyką jest również regularne sprawdzanie poziomu smaru oraz jego stanu, co pozwala na szybką reakcję w przypadku zauważenia jakichkolwiek nieprawidłowości.
Jak często należy smarować narzędzia pneumatyczne?
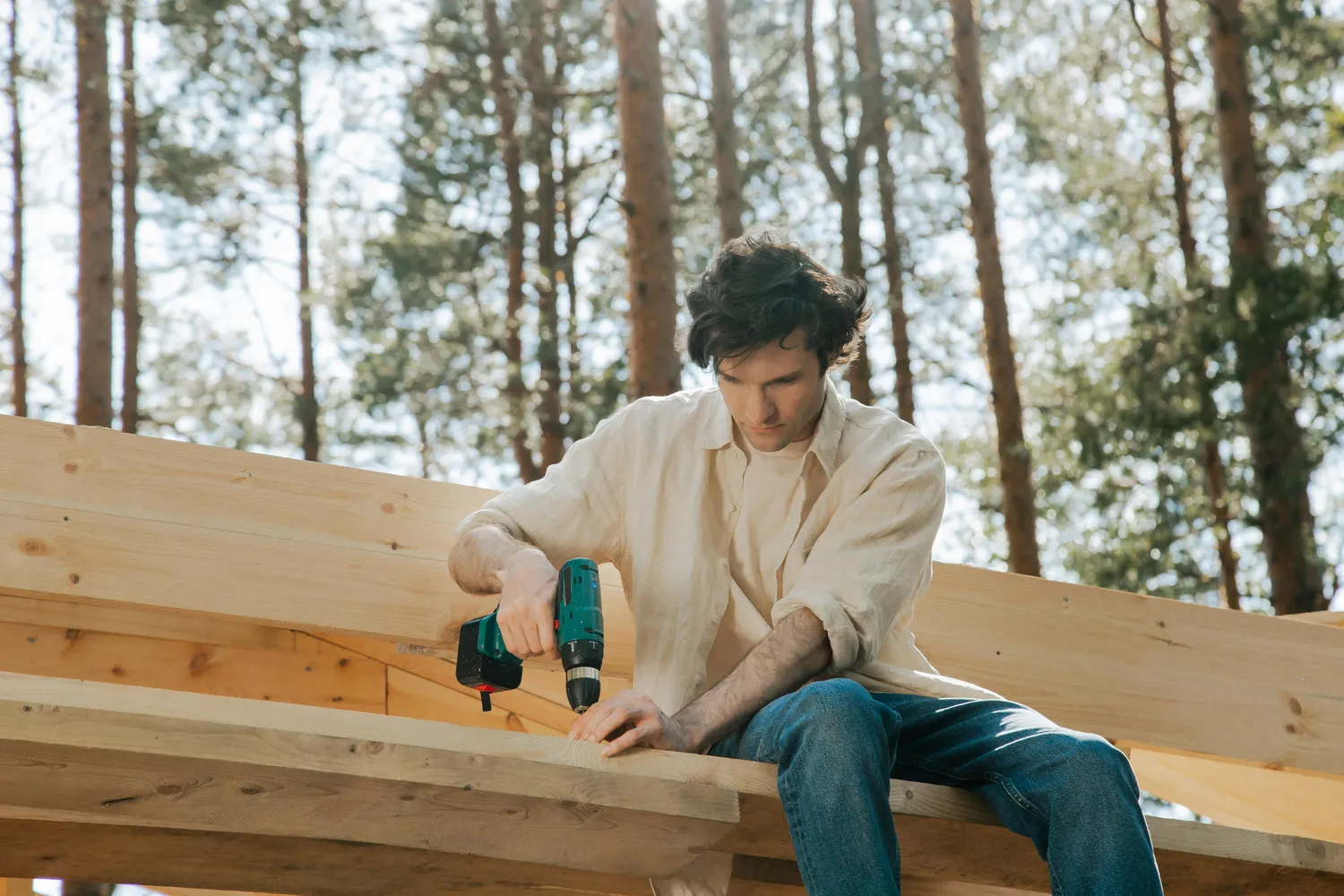
Częstotliwość smarowania narzędzi pneumatycznych zależy od intensywności ich użytkowania oraz warunków pracy. W przypadku narzędzi używanych codziennie w trudnych warunkach zaleca się smarowanie co kilka dni lub nawet codziennie. Z kolei narzędzia wykorzystywane sporadycznie mogą wymagać smarowania raz na kilka tygodni lub miesięcy. Ważnym czynnikiem wpływającym na częstotliwość smarowania jest także rodzaj wykonywanej pracy – na przykład prace związane z dużym obciążeniem mechanicznym mogą wymagać częstszej konserwacji niż prace lekkie. Oprócz tego warto zwrócić uwagę na zalecenia producenta dotyczące konserwacji konkretnego modelu narzędzia pneumatycznego. Regularne przeglądy stanu technicznego oraz kontrola poziomu smaru pozwolą na uniknięcie poważnych awarii i wydłużenie żywotności sprzętu.
Jakie są skutki niewłaściwego smarowania narzędzi pneumatycznych?
Niewłaściwe smarowanie narzędzi pneumatycznych może prowadzić do wielu problemów technicznych oraz obniżenia efektywności pracy. Przykładowo, zbyt mała ilość smaru może powodować zwiększone tarcie pomiędzy ruchomymi częściami urządzenia, co w konsekwencji prowadzi do ich szybszego zużycia oraz ryzyka awarii. Z kolei nadmiar smaru może prowadzić do gromadzenia się zanieczyszczeń i osadów, co również negatywnie wpływa na działanie narzędzia. Ponadto niewłaściwy dobór środka smarnego może skutkować korozją metalowych elementów lub uszkodzeniem uszczelek, co prowadzi do wycieków powietrza i spadku ciśnienia roboczego. W dłuższej perspektywie niewłaściwe smarowanie może skutkować koniecznością kosztownych napraw lub wymiany całego urządzenia.
Jakie narzędzia są niezbędne do smarowania narzędzi pneumatycznych?
Aby skutecznie smarować narzędzia pneumatyczne, warto zaopatrzyć się w odpowiednie akcesoria i narzędzia, które ułatwią ten proces. Podstawowym narzędziem jest pistolet smarowy, który pozwala na precyzyjne nałożenie smaru w trudno dostępnych miejscach. Pistolet smarowy można napełniać różnymi rodzajami smarów, co czyni go wszechstronnym narzędziem. Warto również zainwestować w olej w sprayu, który jest łatwy w aplikacji i idealny do szybkiego smarowania ruchomych części. Kolejnym przydatnym akcesorium jest zestaw szczotek oraz ściereczek, które umożliwiają dokładne czyszczenie narzędzi przed nałożeniem nowego smaru. Dobrze jest także mieć pod ręką różne rodzaje smarów, dostosowanych do specyfikacji poszczególnych narzędzi. Oprócz tego warto posiadać zestaw kluczy i narzędzi do demontażu, aby móc w razie potrzeby przeprowadzić dokładniejszą konserwację lub naprawę urządzenia.
Jakie są najczęstsze błędy podczas smarowania narzędzi pneumatycznych?
Podczas smarowania narzędzi pneumatycznych można popełnić wiele błędów, które mogą negatywnie wpłynąć na ich działanie oraz żywotność. Jednym z najczęstszych błędów jest stosowanie niewłaściwego rodzaju smaru, co może prowadzić do korozji lub uszkodzenia elementów mechanicznych. Innym powszechnym problemem jest nadmierne lub zbyt małe nałożenie smaru, co skutkuje zwiększonym tarciem lub gromadzeniem się zanieczyszczeń. Często zdarza się również, że użytkownicy zapominają o czyszczeniu narzędzi przed nałożeniem nowego smaru, co prowadzi do mieszania się różnych substancji i obniżenia efektywności działania. Należy również pamiętać o regularnym sprawdzaniu stanu technicznego narzędzi oraz poziomu smaru, aby uniknąć poważnych awarii. Warto także zwrócić uwagę na instrukcje producenta dotyczące konserwacji konkretnego modelu narzędzia, ponieważ różne urządzenia mogą mieć różne wymagania dotyczące smarowania.
Jakie są zalety regularnego smarowania narzędzi pneumatycznych?
Regularne smarowanie narzędzi pneumatycznych przynosi wiele korzyści zarówno dla użytkowników, jak i dla samego sprzętu. Przede wszystkim odpowiednia konserwacja wpływa na wydajność pracy – dobrze nasmarowane narzędzie działa płynniej i wymaga mniej wysiłku ze strony operatora. Dzięki temu można osiągnąć lepsze rezultaty w krótszym czasie. Ponadto regularne smarowanie znacząco wydłuża żywotność narzędzi pneumatycznych, co przekłada się na mniejsze koszty związane z naprawami oraz wymianą sprzętu. Utrzymanie narzędzi w dobrym stanie technicznym zmniejsza ryzyko awarii i przestojów w pracy, co jest szczególnie istotne w środowisku przemysłowym czy warsztatowym. Dodatkowo właściwe smarowanie chroni przed korozją i innymi uszkodzeniami mechanicznymi, co zapewnia długotrwałą funkcjonalność urządzeń.
Jakie są najlepsze praktyki przy smarowaniu narzędzi pneumatycznych?
Aby skutecznie dbać o narzędzia pneumatyczne, warto przestrzegać kilku najlepszych praktyk związanych z ich smarowaniem. Po pierwsze, zawsze należy stosować się do zaleceń producenta dotyczących rodzaju używanego smaru oraz częstotliwości konserwacji. Ważne jest również regularne czyszczenie narzędzi przed nałożeniem nowego smaru – usunięcie zanieczyszczeń pozwoli na lepsze przyleganie świeżego środka smarnego i poprawi jego działanie. Kolejną dobrą praktyką jest monitorowanie stanu technicznego narzędzi oraz poziomu smaru – warto prowadzić dokumentację dotyczącą przeprowadzonych czynności konserwacyjnych oraz ich daty. Należy także pamiętać o odpowiednim przechowywaniu narzędzi – powinny być one trzymane w suchym miejscu, z dala od źródeł wilgoci oraz wysokich temperatur.
Jakie są różnice między różnymi rodzajami smarów do narzędzi pneumatycznych?
Na rynku dostępnych jest wiele rodzajów smarów przeznaczonych do narzędzi pneumatycznych, a ich wybór powinien być uzależniony od specyfiki danego urządzenia oraz warunków pracy. Smary silikonowe charakteryzują się doskonałymi właściwościami ochronnymi i odpornością na wysokie temperatury, co czyni je idealnym wyborem dla intensywnie eksploatowanych urządzeń. Z kolei oleje mineralne są często stosowane ze względu na swoje właściwości penetrujące i zdolność do rozpuszczania zanieczyszczeń – świetnie sprawdzają się przy codziennym użytkowaniu. Istnieją również specjalistyczne preparaty przeznaczone do konkretnych modeli narzędzi pneumatycznych, które zawierają dodatki przeciwdziałające korozji oraz poprawiające właściwości smarne. Warto również zwrócić uwagę na biodegradowalne środki smarne, które są coraz bardziej popularne ze względu na swoje korzystne właściwości ekologiczne.
Jakie są objawy niewłaściwego smarowania narzędzi pneumatycznych?
Niewłaściwe smarowanie narzędzi pneumatycznych może manifestować się poprzez szereg objawów wskazujących na problemy z ich działaniem. Jednym z najczęstszych sygnałów jest zwiększone tarcie podczas pracy urządzenia – jeśli operator zauważy trudności w obsłudze lub nietypowe dźwięki wydobywające się z maszyny, może to świadczyć o niedoborze lub niewłaściwej jakości smaru. Innym objawem mogą być wycieki powietrza lub oleju – jeśli ciśnienie robocze spada poniżej normy, warto sprawdzić stan uszczelek oraz poziom smaru w urządzeniu. Zwiększone zużycie elementów mechanicznych to kolejny symptom niewłaściwego smarowania; jeśli części zaczynają się szybciej zużywać niż zwykle, może to oznaczać konieczność przeprowadzenia dokładnej konserwacji lub wymiany środka smarnego.